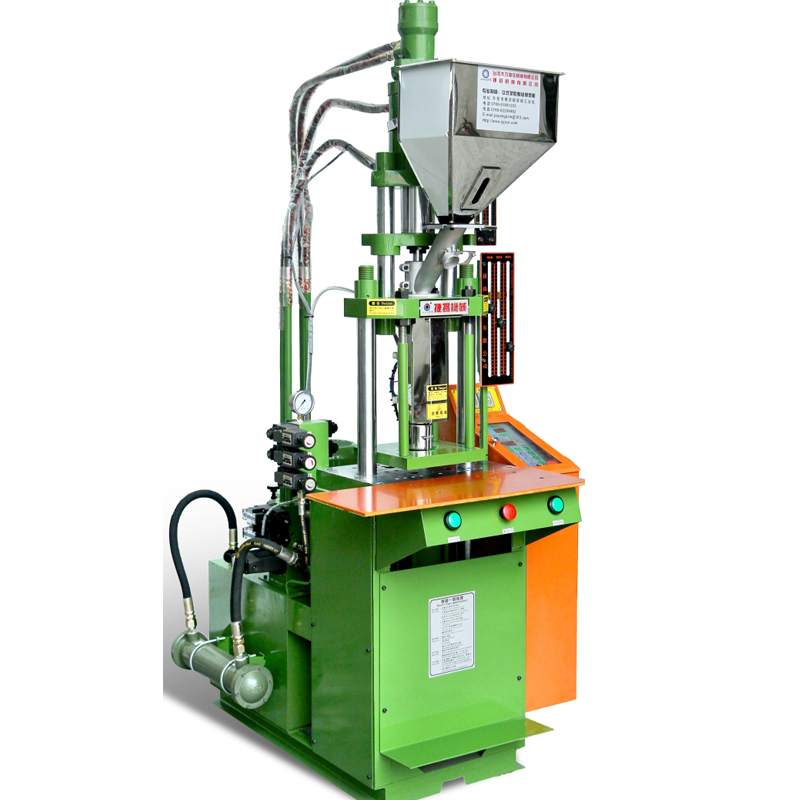
Vertical Injection Moulding Machines is the most common method used to create large numbers of identical items from plastics. Most polymers can used in the process and products produced by injection moulding include bottle lids. Plastic combs, small pieces of furniture and even car door panels. Essentially, the injection moulding process involves feeding plastic polymers in a pelletized form through a hopper into a chamber.
As the material passes along the chamber a rotating screw mixes and melts the material. Once sufficient molten plastic material has collect at the end of the chamber the screw acts as a plunger and the material is inject into a mould, usually made of metal. Moulds are carefully design to reflect the exact requirements of the product being produce. Finally, the plastic solidifies into a shape that has conformed to the shape of the mould. Once cooled slightly, sometimes a robotic arm is use to remove the moulded components but it is more common for the freshly-made items to drop out of the mould into a chute leading to a collection container.
An injection moulding machine is use to manufacture plastic products by the injection moulding process detailed above. There are two main parts to the machines – the injection unit and the clamping unit. In the majority of injection moulding machines the mould is fasten in the horizontal position but moulds can also fitted in the vertical position in some cases allowing gravity to aid the process. Moulds are most commonly fasten to the machine by manual clamps using bolts. But can also fastened using hydraulic or magnetic clamps which both allow for faster tool changes.
Injection moulding machines are rate by tonnage and Shot weight which expresses the amount of clamping force. That the machine can exert to keep the mould close during the process and the maximum weight of article that can moulded. However, machines are primarily classified by the type of driving systems they use namely hydraulic, mechanical, electrical or hybrid. Hydraulic machines are most predominant in most parts of the world with the exception of Japan and were the only option available until 1983. Although widely-used they tend not to be as precise as other machine types. Mechanical injection moulding machines tend to be more reliable than other types.
Electric injection moulding machines decrease operating costs by reducing energy consumption. And also address some of the environmental concerns around these machines. They are more expensive than other types but are quieter, faster and more accurate. Hybrid machines combine the best of hydraulic and electric types but in reality use almost the same amount of electricity to operate as a standard hydraulic machine.
There are many manufacturers/suppliers of injection moulding machines and new advances are being make in the field all the time. And so it is worth researching options and services on offer before making a final decision. See the rest then buy the best BORCHE.